In the arena of modern manufacturing, the
injection molding process has won wide acclaim for its efficiency and precision. However, even the most skillful technique will inevitably encounter challenges. In injection molding parts processing, a common problem is the processing of warpage deformation, which is like a sudden storm, disrupting the original neat and tidy queue. Today, let us explore the secrets behind this storm, to uncover the reasons for injection molded parts warpage deformation.
First of all, we must realize that plastic, this seemingly docile material, in fact, contains a complex and variable character. When it melts at high temperatures, injected into the mold, and then cooled and shaped, it is as if it has undergone a rebirth. In this process, temperature is one of the key factors affecting warpage deformation. If the temperature of the injection mold is not uniform, or the temperature difference during cooling is too large, the plastic shrinkage will be inconsistent, resulting in the accumulation of internal stresses, and ultimately the formation of warpage.
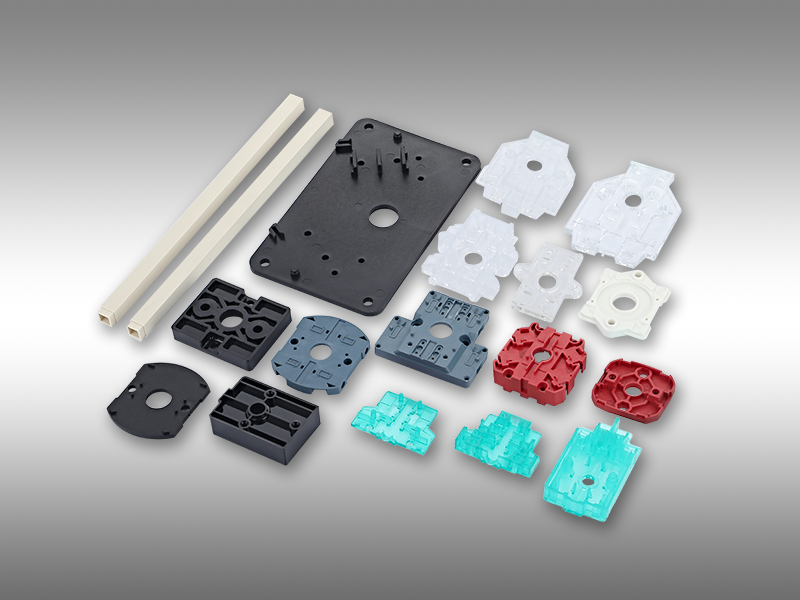
Next, we have to mention the role of pressure. During the
injection molding process, the plastic melt is rapidly pushed to all corners of the mold under high pressure. If the pressure is not evenly distributed, or the holding time is not sufficient, then the plastic will not be filled evenly, thus creating uneven internal stresses during cooling and shrinkage and triggering warping.
In addition, the choice of material is also a profound study. Different plastic materials have different properties, their shrinkage, fluidity and even thermal stability are not the same. If the material is not selected properly, or mixed with impurities, then it is easy to produce defects in the molding process, which will lead to warpage.
The importance of mold design should not be overlooked. A well-designed injection mold ensures uniform filling and cooling of the plastic and reduces internal stresses. On the contrary, if there are defects in the mold design, such as the layout of the cooling waterway is not reasonable, or the exhaust is not smooth, it will become a potential cause of warpage and deformation.
Finally, we have to face the human factor in the operation process. The setting parameters of the
injection molding machine, such as injection speed, pressure, temperature, etc., need to be precisely controlled. The experience and skills of the operator play a crucial role here. The slightest mishap can trigger a domino effect of warpage and deformation.
Like an explorer exploring an uncharted territory, we went deep behind the phenomenon of warpage deformation of injection molded parts to reveal its five major causes: the influence of temperature, the role of pressure, the choice of materials, mold design and human operation. Each warpage is the result of the intertwining of these factors, which together weave a complex cause-and-effect picture.
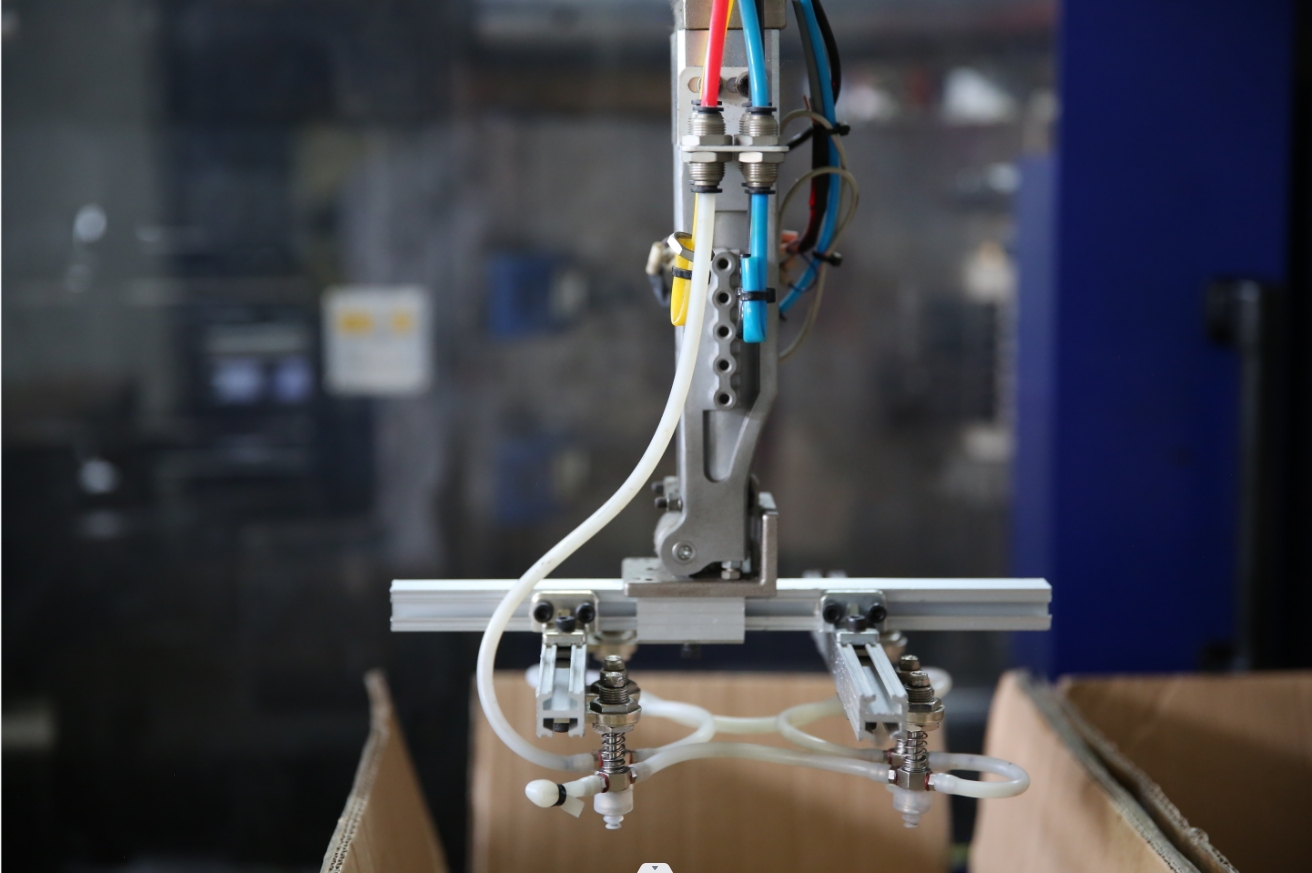
By understanding these causes, we can not only better predict and control warpage, but also take preventive measures during the design and manufacturing process to ensure that every injection molded product is perfectly designed. In this challenging field, every in-depth analysis of a problem is a sublimation of skill, and every experience of solving a problem is a refinement of wisdom.
Let us continue to move forward in the art of injection molding processing, continue to explore, continue to innovate, until every problem is turned into a stepping stone on the road ahead, so that every piece of work becomes a model of industrial beauty.