In the medical field, every innovation is a deep respect for life. The precision and reliability of medical devices are directly related to health and safety. In a field where precision and reliability are at the core, the performance of injection molded parts is especially important. So, how to strengthen the performance of medical device injection molded parts? This is a challenge that combines science, technology and art, so let's explore it together.
First, we must recognize the importance of raw material selection to the performance of the final product. High-quality polymers are the foundation for manufacturing high-performance medical devices. Selecting the right resins for a particular application involves not only considering their mechanical strength, heat resistance and chemical stability, but also ensuring that they can withstand the rigors of the sterilization process. For example, the use of polycarbonate (PC) or polypropylene (PP), which have excellent biocompatibility, ensures a safe and reliable product.
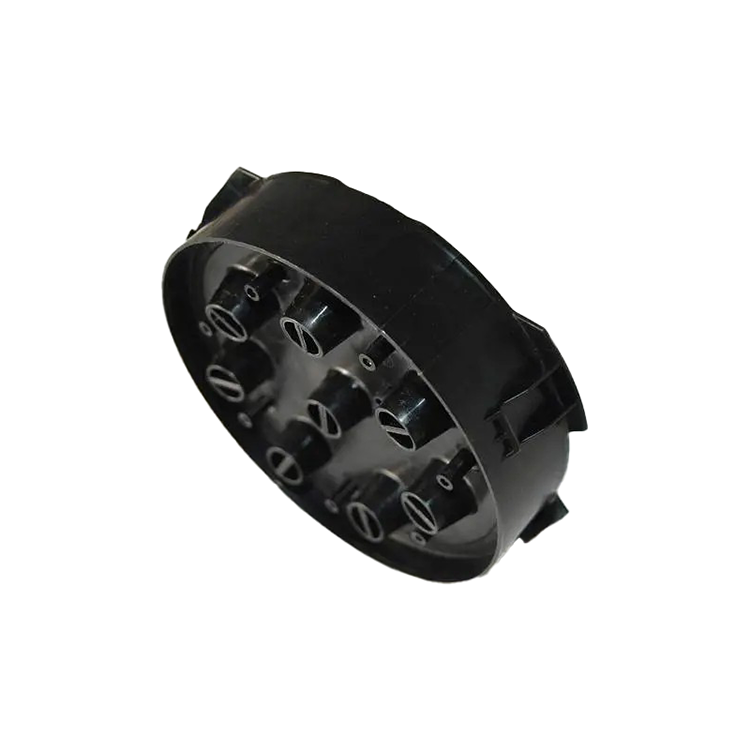
Next, optimization of the injection molding process is key to improving performance. Precise control of melt temperature, injection pressure, holding time and cooling cycle can ensure dimensional stability and physical properties of the molded part. Through mold flow analysis, we can predict and resolve possible defects such as shrinkage, warpage or stress concentration, thus ensuring product consistency and reliability.
In addition, mold design and manufacturing are equally critical. A precise mold not only produces accurately shaped parts, but also ensures perfect surface finish and detail. The use of advanced processing technologies, such as 3D printing and precision CNC machining, allows for the creation of complex and detailed molds, laying a solid foundation for the production of high-performance medical devices.
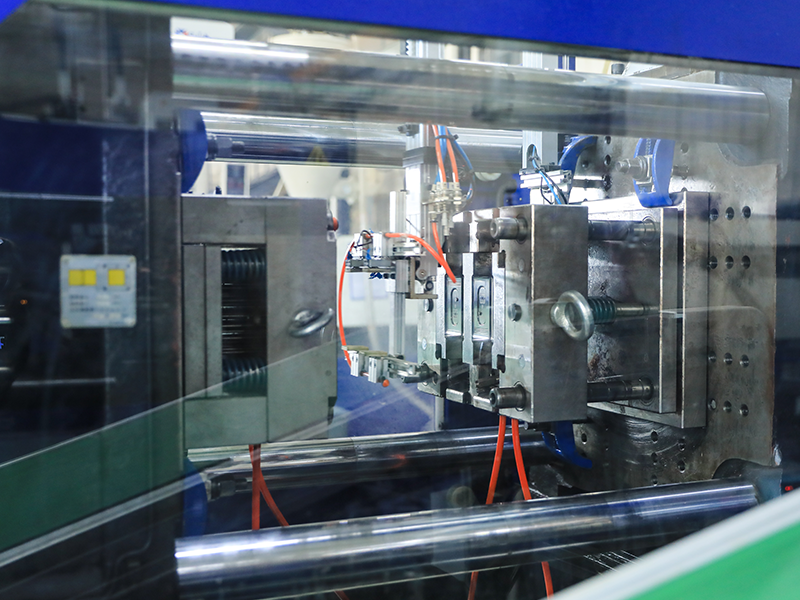
Quality control is also an aspect that cannot be ignored. From raw material inspection to finished product testing, every step must be strictly controlled. Utilizing automated testing equipment and high-precision measuring tools, such as CMMs and optical scanners, product quality can be effectively monitored and problems can be identified and solved in a timely manner.
Finally, continuous R&D and innovation is the driving force behind the performance improvement of medical device injection molded parts. By working closely with medical professionals, understanding clinical needs and continuously exploring new materials, processes and technologies, we can provide patients with safer, more effective and comfortable medical devices.
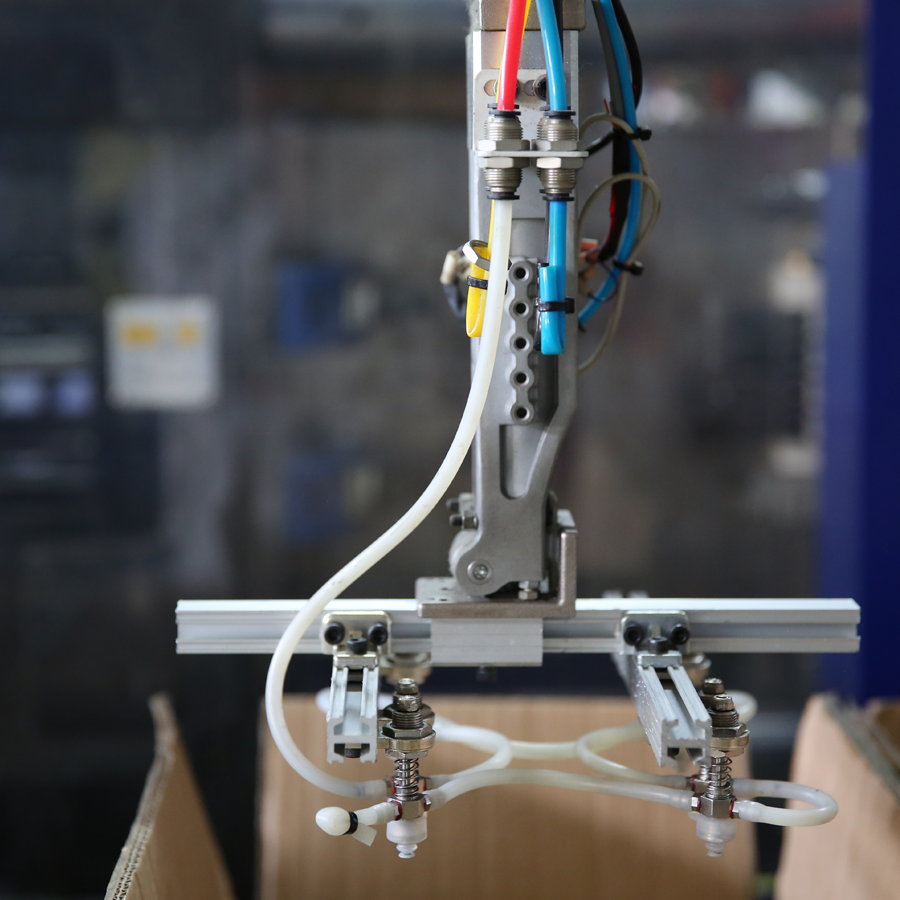
In this pursuit of excellence, every improvement is a respect for life, and every quality medical device is a guardian of health. Enhancing the performance of injection molded parts for medical devices is not only a technical challenge, but also a commitment to be responsible for life. Let's join hands, with the power of science and the exquisite art, to shape a healthier future for the world.