In the blooming of modern manufacturing industry, injection molding processing has become an important process in the manufacture of plastic products with its high efficiency, precision and economy. However, between this seemingly simple injection and molding, there hides a vital secret - pressure maintaining link. It is like a delicate brush, outlining the soul of the plastic product and determining the texture and performance of the product. Today, let's explore the invisible hand that shapes perfection in the world of high-temperature molten plastics.
Pressure retaining, as the name suggests, is the process of injecting plastic into a mold cavity and then continuously applying a certain amount of pressure so that the molten material is able to replenish the voids created by shrinkage before it cools and solidifies. This process is like an artist putting the finishing touches on a piece of artwork, where the smallest details make the difference. Precise control of the holding pressure is the key to ensuring the quality of the product.
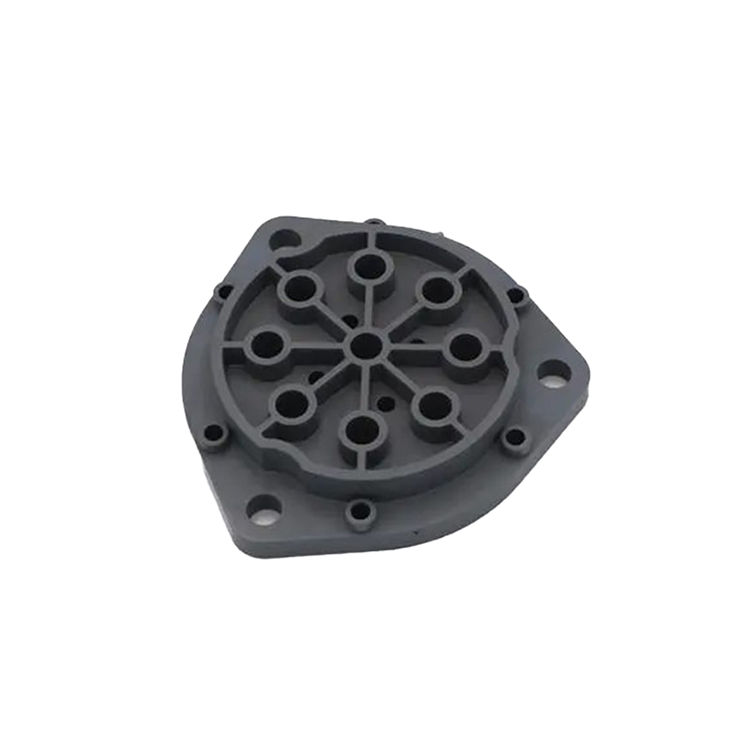
In the process of keeping pressure, the mastery of time and pressure is an esoteric art. The length of time directly affects the internal structure and appearance of the product, and the difference of one second may be the difference between flaws and perfection. The size of the pressure, like the sculptor's hand strength, too light is difficult to fix the shape, too heavy may lead to product deformation or even damage. Only the right amount of pressure can make the plastic molecules closely aligned to form a strong and uniform structure.
The importance of holding pressure is not only reflected in the physical level, but also lies in its far-reaching impact on the performance of the product. The strength, toughness and abrasion resistance of a product that has been carefully pressurized will be significantly improved. This is like putting an invisible armor on the product, making it more durable in daily use and more resistant to external challenges.
However, pressure retention is not a static process. As a product's design varies, so does the required holding pressure strategy. This requires the injection molding engineer to act like a conductor, adjusting the tempo of the ensemble (pressure retention parameters) according to the different pieces of music (product design) in order to achieve the most harmonious results. Each adjustment is a deep understanding of the nature of the material and a precise grasp of the molding laws.
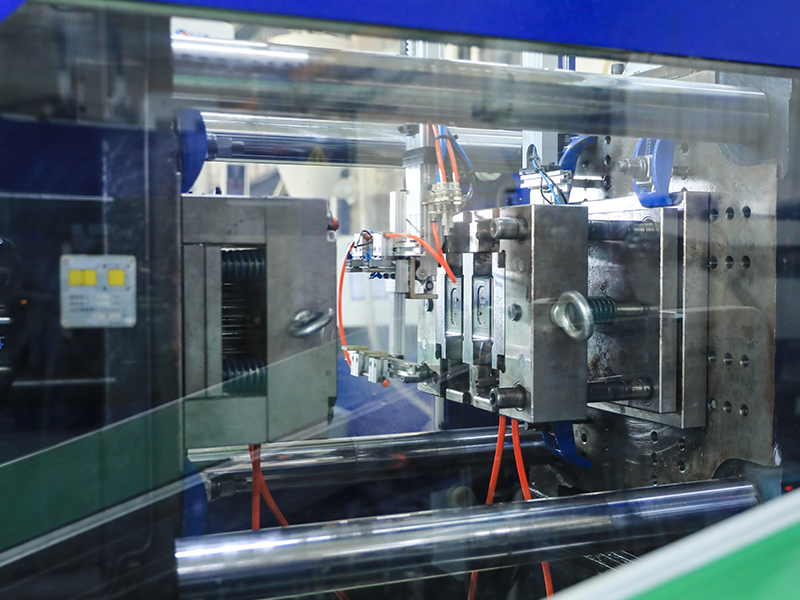
In today's increasingly environmentally conscious world, pressure maintaining also carries the mission of green manufacturing. Proper holding pressure can reduce the waste of materials, lower production costs, and also reduce the impact on the environment. This is not only a technological advancement, but also a responsible reflection of the future.
In short, the importance of the holding pressure link in the injection molding process is self-evident. It is like the sculptor's last cut, the painter's last brushstroke, determining the product from ordinary to excellent metamorphosis. In this seemingly simple link, contains profound scientific principles and exquisite craft art. Every success of pressure preservation is a respect for material, technology and responsibility, and a careful carving for a better life in the future.
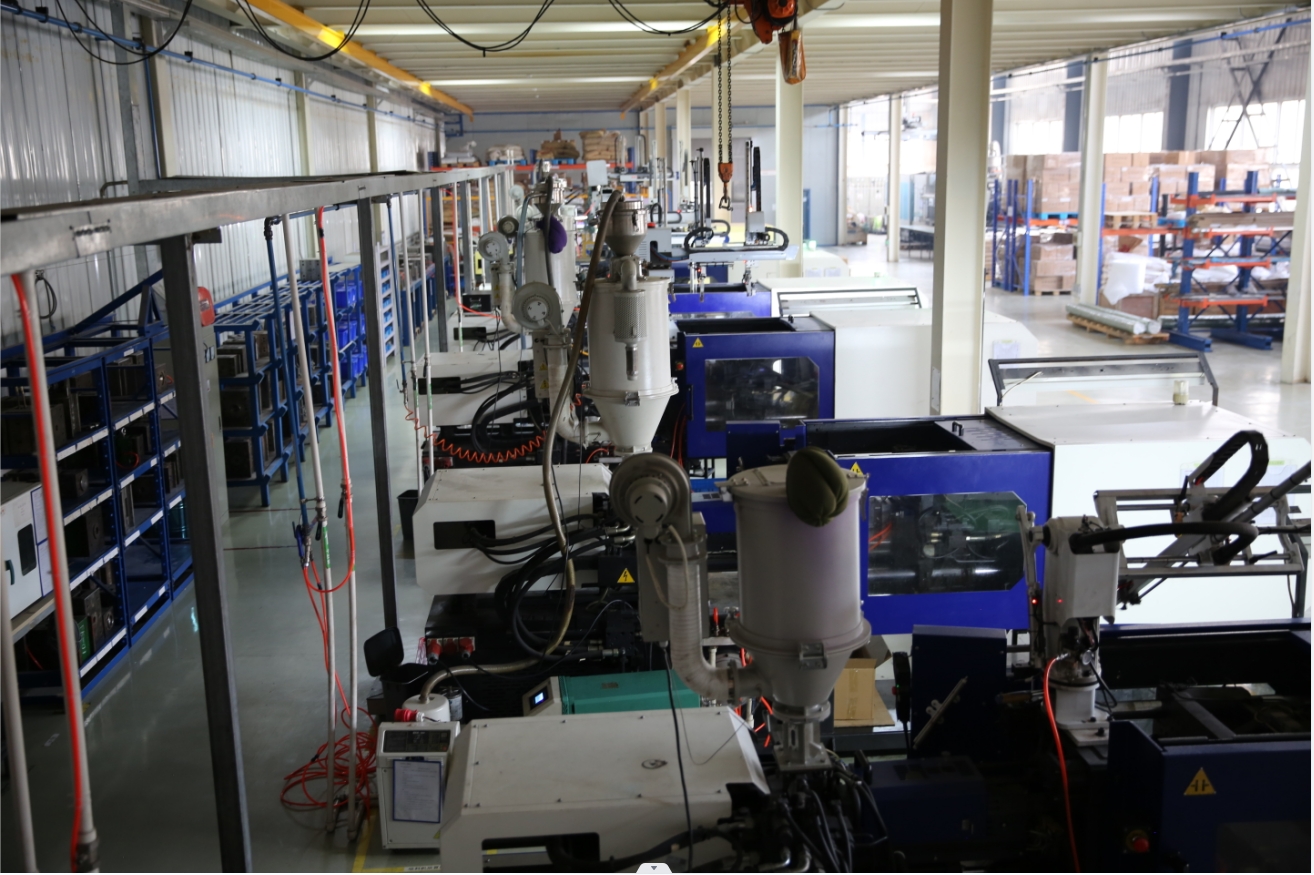
In the future, with the continuous progress of science and technology, the pressure preservation technology will also continue to innovate to adapt to the more complex and changing market demand. But what remains unchanged will be the craftsmanship of excellence in this process and the relentless pursuit of perfect quality. Let us look forward to, under the subtle interpretation of pressure preservation, more excellent plastic products, like art, into our lives, beautify our world.