In the world of plastics processing, injection molding is a masterful craft, like an artist splashing colors on a canvas to create a precise and vivid part. Today, we're going to explore a key step in this art: how to set the shot cylinder temperature and melt temperature in injection molding.
First, let's understand why temperature control is so important. During the injection molding process, the plastic material needs to be heated to a certain temperature in the injection cylinder to transform it from a solid state to a molten state. This transformation is not a simple physical change, but a perfect dance of chemistry and physics. If the temperature is too low, the plastic will not be able to melt completely, resulting in incomplete molding or even short shots; if the temperature is too high, it may result in the decomposition of the plastic, affecting the strength and appearance of the product.
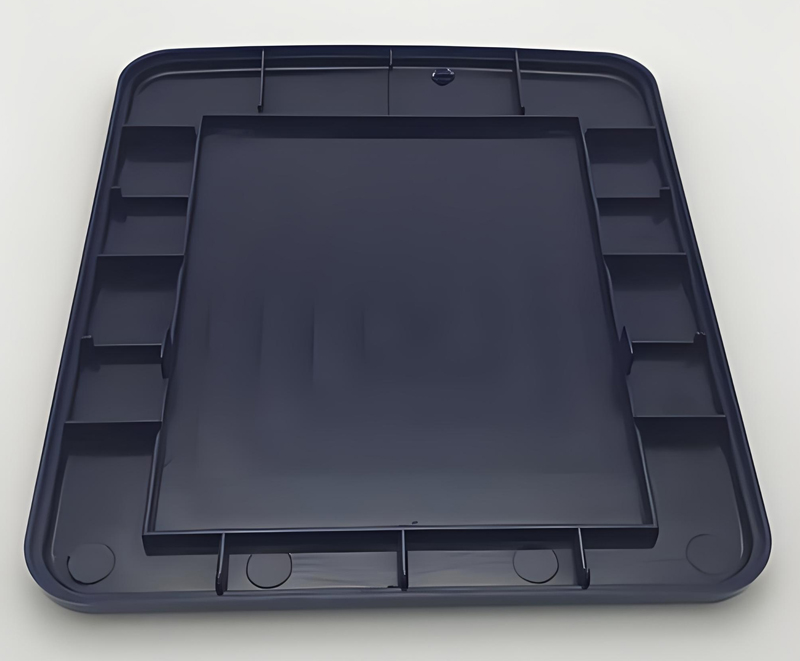
So, how to determine these two temperatures? This requires an in-depth understanding of the nature of the plastic material. Each plastic has a specific melting range, which is determined by its molecular structure. For example, polyethylene (PE) and polypropylene (PP) usually melt between 160°C and 250°C, whereas polycarbonate (PC) and polyamide (PA) require higher temperatures, usually between 240°C and 300°C.
When setting the temperature of the injection cylinder, we usually set a temperature slightly above the melting point of the plastic to ensure that the plastic melts evenly and thoroughly. At the same time, we need to take into account the thermal stability of the plastic during the heating process, as well as its cooling rate in the mold. Therefore, the temperature setting of the injection cylinder is a process that takes into account the material properties, product requirements and production efficiency.
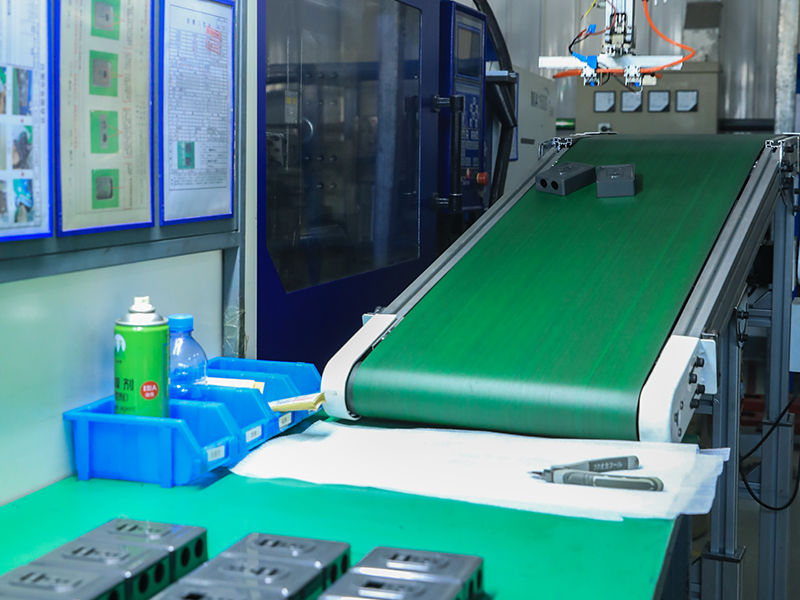
As for the melting temperature, it is the last stop for the plastic before it enters the mold from the injection cylinder. Here, the molten plastic needs to remain fluid enough to be able to fill every corner of the mold. The melt temperature should be set slightly above the shot cylinder temperature to ensure this fluidity. However, too high a melting temperature may cause the plastic to degrade and affect the quality of the final product.
In practice, we usually determine the optimum temperature setting through a series of tests. These tests include flow rate tests, melt index measurements and actual injection molding trial runs. Through these tests, we can observe the behavior of the plastic at different temperatures to find that perfect balance.
In conclusion, setting the injection cylinder temperature and melt temperature is an art in injection molding that requires a deep understanding of the material and fine control of the process. When we have mastered this art, we will be able to mold the plastic into whatever shape we have in mind, like a sculptor, creating one stunning piece after another.